How To Implement Lean Management in IT: A Case Of Utrace
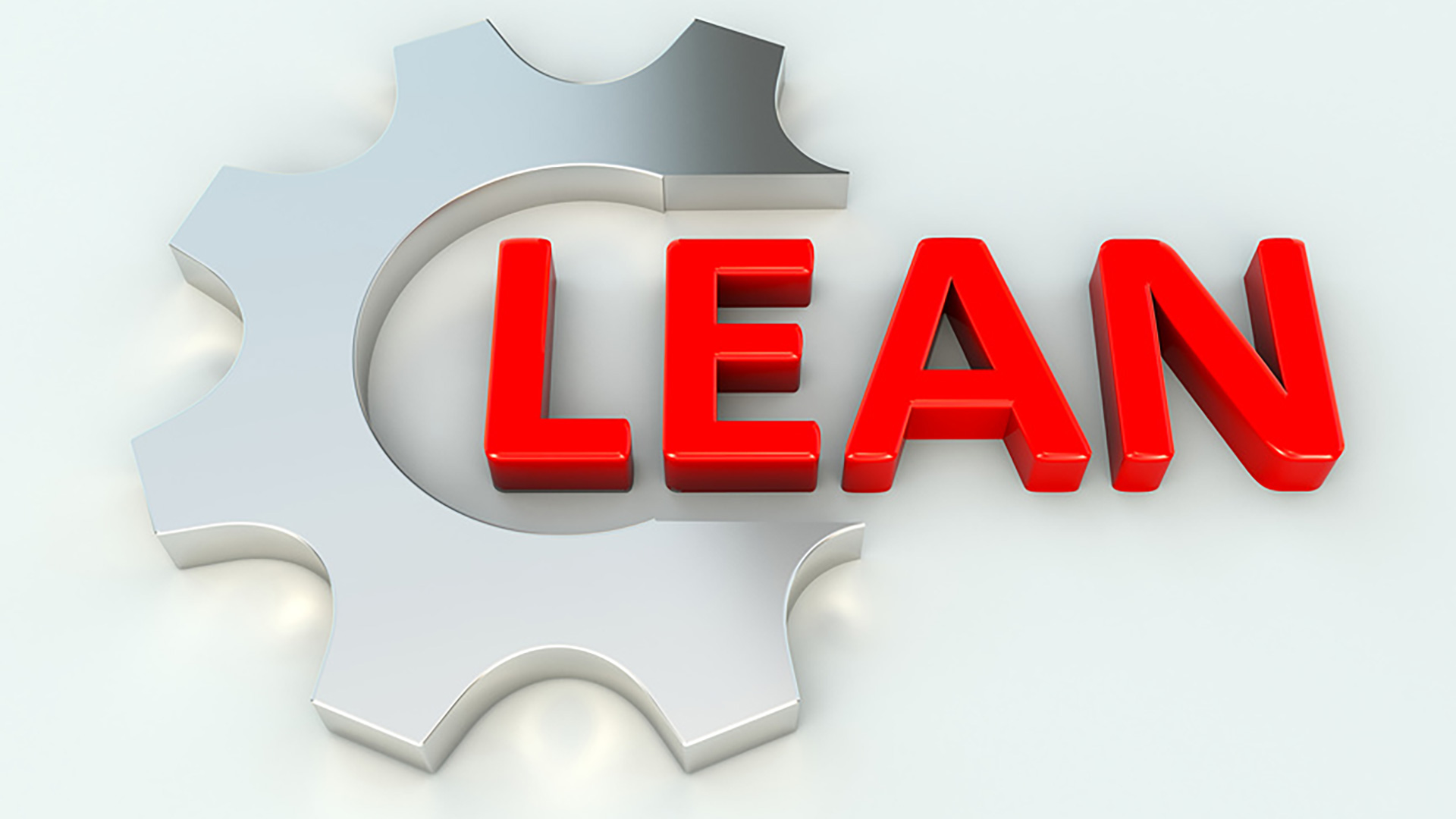
Lean management has become a popular approach for companies looking to optimize their operations and improve quality. We asked Arif Gadzhiev, development director at Utrace, to explore how the company implements the principles of this approach in both product development and customer service.
Why does a company need a lean management approach?
The interest in lean manufacturing or management has not diminished since the publication of "The Machine That Changed the World" by James Woomek, Daniel Jones, and Daniel Russ in 1990. The book revolutionized the idea that a company's success depends not on expensive equipment but on effective process management.
According to the concept, a mature company deeply understands its business processes. The team systematically measures and evaluates these processes. It prevents possible errors. In case of a failure, the team's task is not only to fix it but to identify the root cause and find out if it is related to processes, equipment, people, or some complex problem. This approach helps avoid the possibility of recurrence of failure and minimize financial and reputational losses.
The framework of lean management has expanded beyond industrial enterprises and taken root in many industries. This adoption has led to its implementation in many organizations, including our company.
Implementing Lean Production
In Utrace, we implement the concept of lean management in two ways. Firstly, on the product side, we launch Root Cause Analysis (RCA) and Problem Management procedures for recurring or product-related incidents. We evaluate the entire process, not just the specific part where the issue occurred. It helps to identify the stage at which the failure occurred, the quality of input data, user actions, and other details. analysts use this information to suggest improvements to the system, thus reducing the likelihood of product failures.
Secondly, we have extended the lean management approach to customer service. Commonly, users report failures to the hotline, and technical support is provided through either HelpDesk, which is focused on incident management, or ServiceDesk, which provides services on request, including troubleshooting. However, our approach is distinct. We prioritize a preventive search for potential problems. During their downtime, our specialists work on detecting possible errors, such as monitoring the client's stands, carrying out tests, and identifying vulnerabilities. This allows us to take a proactive approach to resolving issues, rather than simply reacting to them after they occur.
Furthermore, our specialists don't just address bugs when conducting an analysis, they also delve into the root cause of the issue. The underlying problem may stem from the company's logistics processes, such as a brief interval between receiving and circulating goods, resulting in the regulatory system receiving simultaneous messages that disrupt their sequence. When an incident is detected, we conduct checks for similar errors in other clients. To achieve a zero-incident rate, we implemented the Zero Accident Vision (ZAV) strategy, which includes active monitoring rules. As a result, our preventative approach has yielded significant outcomes.
Things don't always go smoothly
Moving to lean management can present significant challenges, especially when it comes to ensuring that everyone involved in the product or process has a stake in the outcome. Success heavily relies on their active participation, and even minor errors could derail the entire effort. For established international companies, the lean management approach has been well-developed over decades, with most conceptual issues already resolved. New employees naturally adopt the lean production paradigm and work within a company culture that values it. However, for businesses new to lean management, it's crucial to cultivate a culture that emphasizes the importance of taking responsibility for the product or service and encourages employees to participate in process improvement.
This challenge was approached in Utrace by making customer service the starting point for building a lean management culture. We provide new employees with training in ServiceDesk, which focuses on developing skills like taking the initiative, problem-solving, and a desire to learn and grow. After that, we help them build a career path within the company.
The second challenge is to justify support service fees in zero-incident case. Clients may question why they're paying if they're not experiencing issues. One solution is to revise contractual provisions to include active monitoring, proactive incident detection, and a plan to reduce appeals. We also report on the amount of work done to prevent incidents and the changes made to the product based on active monitoring. It helps clients to understand that they pay for solutions and preventive measures to avoid future issues. By making the process more transparent to customers, we can ensure that our lean management approach is well-received and understood.
Vendors move to lean manufacturing too
For many years, IT vendors have been working on a reactive principle of dealing with customer requests. Whenever a problem arises, it is logged and resolved by the ServiceDesk. In most cases, the process outsourced, and external teams are often evaluated by the number of incidents they have resolved. It is not financially beneficial for them to focus on preventing potential issues from occurring.
However, more companies begin to understand that proactive services provide a competitive edge for both product and clients. It is especially true in the modern highly competitive environment, with growing business risks and economic instability. In the next 3-5 years, most IT companies will completely shift their services to lean management, focusing on preventing problems before they occur.